Every c-store owner must control shrinkage and meet customer demand with a regular inventory cycle count. Not only will you keep shelves stocked with high-selling items, but you can keep your eye on high-theft items as well. And, as you know, inventory placement optimization will help increase your profitability.
Smart idea: Creating cycle count tickets through Petrosoft’s cloud-based back-office system, CStoreOffice®, allows you to spot store errors quickly and eliminate future errors from occurring.
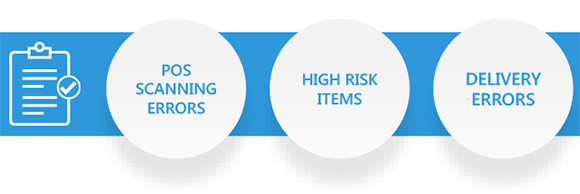
What is a cycle count?
A cycle count is an easy way of placing physical inventory counts on a cycle based on certain factors, including the item or category’s turnover rate, level of risk, and any errors encountered through scanning at the point of sale. Cycle count tickets make it simple for you to accurately track item-level inventory within any of your store locations at any time. Once you process a ticket, an “Item Shortage Report” will be produced to show you where your store has overages or shortages.
How are cycle counts used?
- Control point-of-sale (POS) scanning errors and keep inventory numbers in check. Monitor vendors to ensure inventory needs are met and an explanation is given for overages or shortages. For example, you can correct an invoice entered incorrectly, ensure buy downs are set up accurately, or make sure spoilages are entered into the system properly.
- Review every invoice to make sure there are no errors.
Try this: Use Petrosoft’s cloud-based back-office system, CStoreOffice®, to control inventory shrinkage and meet your customers’ demands with a consistent inventory cycle count. You’ll find practicing inventory placement optimization will boost sales and increase profitability.